What is EDI?
Sep 01, 2018
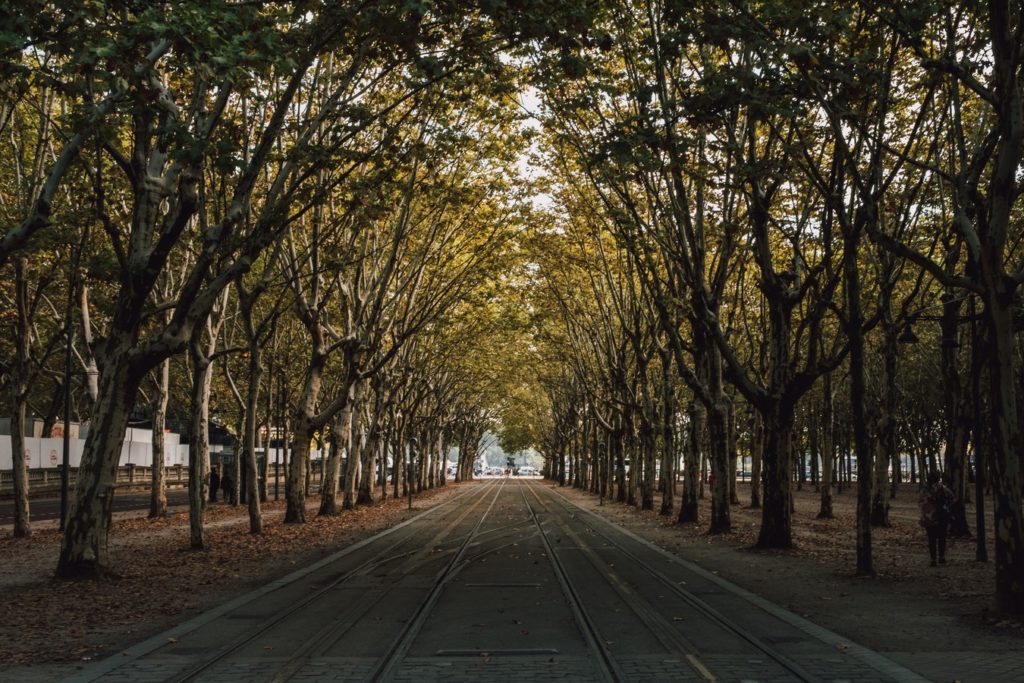
Abbreviation EDI stands for ’electronic data interchange’. There is no need to send business documents on paper or as PDF-files via email anymore. EDI enables transfer of e-documents that move between business partners’ ERP systems automagically, from computer to computer.
The magic is hidden in e-document format. In order to be computer-processed, a document has to follow predetermined structure. As you perhaps have noticed, invoices that pop into your mailbox as PDF-files don’t follow one specific predefined structure – that is why PDF-documents are not true e-documents.
Why should companies automate business processes?
There could be more than ten documents involved in a single business transaction. Simply said, goods need to be ordered, collected and sent, as well as someone has to receive and pay for them. Each step of the process may add a new document to the transaction. From the buyer perspective we are talking about a process which starts with a purchase and ends with paying. From the vendor point of view, it is a process from order to money collection. In both cases, EDI increases the efficiency of the whole supply chain. As there is no need for double data entry anymore, manual labor will reduce remarkably, as well as the amount of human errors.
Some ten years ago, in the Baltics, electronic data interchange could have been something innovative. Today, however, it is rather a standard. The more companies automate business processes, the greater are the benefits to be gained.
How does electronic data interchange work?
The most common e-document types are orders, purchase invoices and sales invoices. It is also possible to automate despatch and receive advices, and return announcements information flow, for example. Using EDI, initiating a document happens in ERP and this is the only time that requires data entry, as usual. E-documents move through an operator (e.g. Telema) whose task is to “translate” the documents into a proper format and structure for receiver’s system. Recipients can start processing information in their ERP immediately, there is no need to re-enter any of the data manually. Employees can thus create more value by concentrating on activities that make the difference for the company!